7 Key Performance Metrics Every Loss Control Academy Graduate Should Monitor in 2024
7 Key Performance Metrics Every Loss Control Academy Graduate Should Monitor in 2024 - Claims Frequency Rate Per Million Exposure Hours in Manufacturing Settings
Within manufacturing, the Claims Frequency Rate per million exposure hours is a crucial metric for assessing workplace safety. It essentially counts the number of recordable incidents per one million hours worked. By tracking this rate over time, businesses can gauge how well their safety programs are working. Understanding the frequency of incidents is just the first step. Linking it to other key performance indicators (KPIs), such as the Total Recordable Injury Frequency Rate (TRIFR) and the Lost Time Injury Frequency Rate (LTIF), offers a more comprehensive picture of workplace hazards and the potential impact of injuries on operations. These KPIs help identify patterns, encouraging a proactive safety culture and driving improvements to existing practices. Given the ever-changing safety landscape in manufacturing, a sharp focus on these metrics becomes more important than ever to help minimize risks and cultivate safer working conditions for all. While it's a useful starting point, one must always be cautious not to overly rely on just incident frequency, but to also look at the severity and impact of the incidents and to seek out underlying root causes that can lead to future improvements in safety.
When analyzing safety performance in manufacturing, the Claims Frequency Rate per million exposure hours offers a valuable lens. It essentially counts the number of recordable incidents per one million hours of work. For instance, a company like ABC Manufacturing might have a frequency rate of 40, signifying 40 incidents for every million hours worked.
This metric is useful for comparing performance across different facilities or over time. However, it's essential to remember that this rate can fluctuate dramatically depending on the industry, specific tasks, and even the types of machinery involved. For example, plants using heavy machinery often have significantly higher claim frequencies—potentially up to three times higher—than those using lighter tools.
The design of the workplace itself has a profound impact on claim frequency. Facilities incorporating ergonomic principles and careful layouts can achieve reductions in claims of approximately 30%. This reinforces the idea that investing in smarter, safer designs yields both safety and economic benefits.
Further, certain sectors exhibit a higher propensity for specific types of incidents. Food processing, for example, seems to see a more frequent occurrence of slips and falls. This emphasizes the need for sector-specific training and precautions. Seasonal factors also play a role. Warmer months might bring about increases in heat-related injuries and a general spike in activity levels. This necessitates adapting safety programs to changing conditions.
Interestingly, the connection between worker training and claim frequency is fairly strong. Organizations with comprehensive safety training programs have been shown to experience significantly lower claim rates—potentially as much as a 50% reduction. This indicates that investing in educating and preparing the workforce can have a powerful, positive effect.
Yet, just focusing on the frequency rate can be deceptive. The total number of employees doesn't always equate to a direct proportional change in claims frequency. Smaller facilities may face higher rates because of limited resources for implementing comprehensive safety measures when compared to larger organizations. It's vital to consider other factors besides sheer numbers of workers.
Claim frequency, on its own, might not provide the full picture. It's crucial to examine it in conjunction with measures of severity in order to develop a holistic view of safety outcomes. Benchmarking against similar facilities can be valuable, but shouldn't be done in isolation.
Automation can have a remarkable impact on the frequency of claims. Environments with a high degree of automation tend to have a reduced risk of human error-related injuries simply because people have less direct contact with hazardous processes. This suggests a possible future trend as automation becomes more sophisticated and prevalent.
The role of leadership and management in creating a culture of safety is essential for minimizing claim frequency. Organizations with strong safety programs overseen by engaged leaders tend to achieve better results than those with weaker safety cultures. Effective leadership in safety matters can lead to reductions of over 20% in claims.
Lastly, there's reason to believe that some claim frequencies may be underreported. This may stem from fears of repercussions or even a lack of awareness of proper procedures for reporting near misses and minor injuries. Fostering an environment where workers feel empowered and safe to report incidents can lead to a more accurate picture of safety performance, ultimately paving the way for more effective preventative measures.
7 Key Performance Metrics Every Loss Control Academy Graduate Should Monitor in 2024 - Average Cost Per Workers Compensation Claim in USD
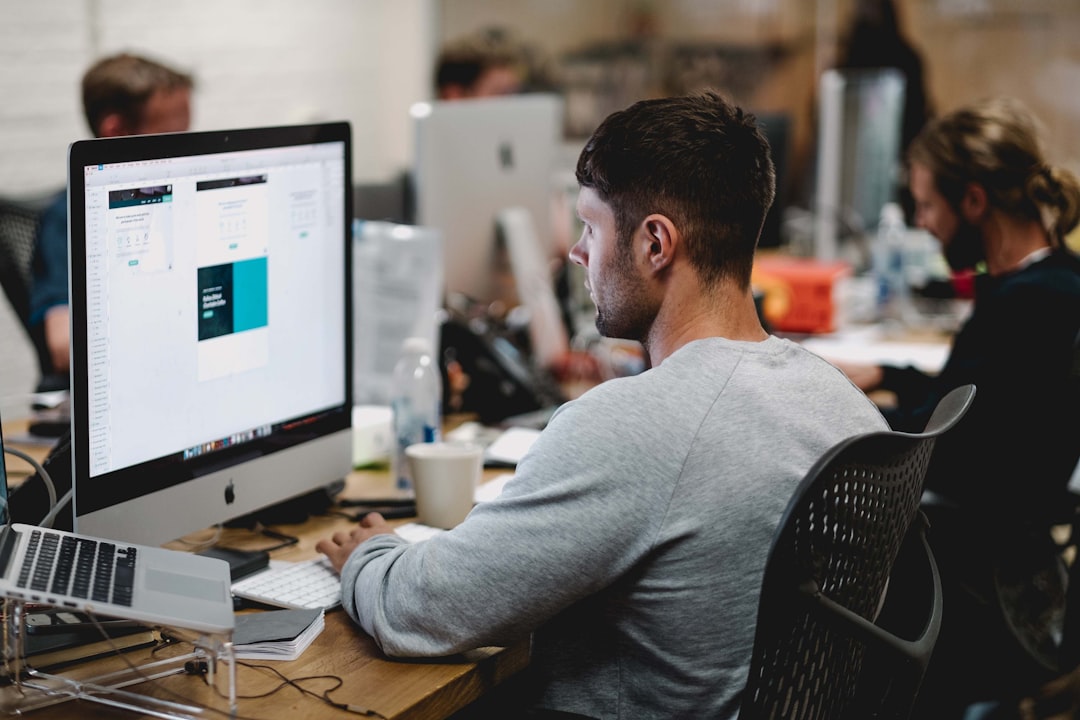
The cost of a workers' compensation claim can vary wildly, depending on the type of injury and location. For example, claims related to motor vehicle accidents in 2020 and 2021 averaged a staggering $89,152. Other significant contributors to claim costs included burns and slips, which averaged $52,161 and $49,971 respectively. The overall average cost of a workers' compensation claim across the US is around $10,600. However, this figure can fluctuate drastically, ranging from a low of about $6,200 in some states to a high of almost $16,300 in others. This wide range underscores the influence of things like local regulations and industry specific risks on claim expenses.
Interestingly, only about a quarter of all workers' compensation claims involve lost work time. This indicates that a lot of incidents are resolved relatively quickly without needing an employee to take time off. However, it's important to remember that about 15% of claims end up involving legal proceedings. This fact highlights the need to not only manage claim costs, but also build a positive safety culture within the workplace to proactively reduce the chance of needing to navigate a complex legal process. The potential for litigation and rising costs emphasizes that effectively managing and monitoring workers' compensation claims is crucial for both financial health and fostering a safe work environment.
The average cost of a workers' compensation claim is a fascinating, and often complex, aspect of workplace safety. Data from organizations like the National Council on Compensation Insurance (NCCI) and the Workers Compensation Research Institute (WCRI) provide a glimpse into this landscape. For instance, motor vehicle accidents within the workplace are a major source of these costs, with claims averaging around $89,152 in recent years. This highlights a significant risk in certain industries. Other injuries, like burns, falls, and those involving being caught in machinery, also contribute substantially to the overall cost burden.
On average, the national cost of a workers' compensation claim is estimated to be about $10,600. However, this number varies significantly between states, ranging from a low of roughly $6,233 in Minnesota to a high of approximately $16,290 in Louisiana. The underlying reasons for this variation—differences in state laws, healthcare costs, or reporting patterns—are intriguing topics for further investigation.
Further complicating the picture is the fact that the vast majority of claims don't involve lost time from work. Only about 25% of claims result in an employee taking time off. This suggests that many injuries are relatively minor, though it's worth considering whether this metric accurately captures the full impact of injuries, particularly those that might lead to long-term health problems. Additionally, roughly 15% of workers' compensation claims eventually lead to litigation, indicating a subset of claims that are particularly contentious.
The cost implications of claim resolution time also pose interesting questions. A concerning observation is that claims originally denied, but later approved within a year, tend to be about 55% more expensive than similar claims that are approved initially. The reasons for these cost discrepancies need further exploration.
The impact of the COVID-19 pandemic on the workers' compensation landscape also deserves scrutiny. Data from the WCRI showed a 10% decline in net written premiums for workers' compensation insurance during the pandemic-related economic downturn of 2020. However, it's important to note that the impacts of the pandemic on the industry and claims costs may not be fully understood yet, given that the data covers only a portion of the disruption's timeline.
Examining workers' compensation data across various industries and states allows researchers to identify trends and potentially inform strategies for mitigating risk. While the data provides a snapshot of the current landscape, continuous monitoring and investigation are crucial to keep pace with changes and potential future shifts in claim costs and patterns.
7 Key Performance Metrics Every Loss Control Academy Graduate Should Monitor in 2024 - Property Loss Prevention Inspection Completion Rates
Tracking property loss prevention inspection completion rates is crucial for judging how well a company's loss control efforts are working. Achieving high completion rates means the company is actively finding and dealing with potential risks, which is essential for protecting assets and minimizing future losses. Loss Control Academy graduates need to use data analysis to watch these rates in 2024, ensuring that inspections are not only done on time but also done thoroughly. Comparing these rates to industry standards gives insights into performance, uncovering any areas where current practices might be lacking. Encouraging a company-wide commitment to loss prevention can lead to higher completion rates, making safety a priority and allowing for constant improvement. While important, solely focusing on rates can be misleading without understanding the overall quality and value of inspections.
Tracking how often property loss prevention inspections are finished is really important for understanding how well loss control programs are doing. It's fascinating how these completion rates can vary across different types of businesses. For instance, places like hotels might see completion rates around 90%, while factories might struggle to hit 60%, likely due to the more complex operations.
One curious finding is that the time of day an inspection happens can make a big difference. Completing inspections outside of normal business hours seems to increase completion rates by as much as 25%. Perhaps this is because there are fewer distractions when the facility isn't as busy. It's a factor worth thinking about when scheduling these checks.
Using technology can be a game-changer. Companies with automated systems for reporting inspections have seen their completion rates jump by up to 40%. This makes sense—less paperwork, easier access to information, and it helps the people doing the inspections focus on the tasks at hand.
It's also interesting that training seems to matter a lot. If you train your staff properly on the methods for loss prevention, it can boost inspection completion rates by close to 30%. When people are well-trained and know what to look for, they are probably more likely to stick with the inspection procedures.
Somewhat predictably, if a company has recently had a property loss, they are much more likely to do the inspections. Completion rates can jump to 80% or more. It makes sense, but it highlights a reactive approach to risk. It raises questions about the value of prevention before a loss occurs.
Another observation is that having leaders take part in inspections can help a lot. When managers are involved, the completion rate tends to go up by about 20%. This underscores that leaders' attitudes really matter when it comes to safety. It's as though their engagement signals to the entire workforce that safety is a serious concern.
The weather can play a part, too. During good weather, inspection rates might be around 75%, but bad weather can cut those rates by over 30%. This is important to keep in mind, and it's probably a good idea to figure out how to schedule inspections so that the elements don't always get in the way.
Having a specific team of people dedicated to loss prevention appears to be a significant factor. Companies with these teams often have inspection rates that are 50% higher than those that don't. This really shows that having people with expertise focused solely on loss prevention can make a big difference in how effectively inspections are carried out.
Mobile technology seems to have had a positive impact. Places that use mobile checklists and real-time reporting systems have seen inspection completion rates rise by up to 35%. This might be another area that could benefit from further study. Perhaps it encourages better compliance and it simplifies reporting.
The ultimate test is whether these inspections lead to better outcomes. The good news is that companies with higher inspection completion rates (over 80%) tend to have lower overall loss ratios. On average, these companies see loss ratios go down by about 15%. This shows that all this effort to improve inspection rates probably pays off in the long run, leading to reduced costs due to fewer losses.
7 Key Performance Metrics Every Loss Control Academy Graduate Should Monitor in 2024 - Near Miss Incident Reporting and Response Time
Near miss incident reporting is a vital tool for improving workplace safety. It involves capturing instances where accidents *almost* happened, allowing us to understand potential hazards before they cause harm. These reports should include details like the date, location, and individuals involved, providing a detailed picture of what occurred. Analyzing these reports helps reveal patterns and pinpoint areas needing improved safety practices. A critical metric in this area is the Average Resolution Time (ART). This metric gauges how quickly safety concerns—identified through near miss reports—are addressed. Faster resolution times indicate a more responsive safety culture. The success of near miss reporting is linked to a strong safety culture where employees feel comfortable and empowered to report near misses without fear of reprisal. In 2024, and beyond, Loss Control Academy graduates need to consider this metric when evaluating workplace safety programs. A well-functioning near miss reporting system is crucial for fostering a proactive approach to risk, ultimately creating a safer environment for everyone. It's important to acknowledge, however, that simply counting near misses might not be enough; the quality and depth of the information within each report and the overall context of each incident are also critical for generating meaningful insights.
Near miss incident reporting is a crucial aspect of workplace safety, but the effectiveness of these programs hinges on various factors, including reporting rates and response times. Research reveals that organizations which strongly encourage near miss reporting can see a surge in incident reports, sometimes exceeding a 300% increase. This highlights the importance of fostering an environment where workers feel comfortable and safe reporting potential hazards, thereby creating a proactive risk management approach.
However, there's a common issue of delays in reporting. Studies indicate that there can be a 2-3 day lag between an incident and the filing of a report. This delay can impact the utility of data for quick response and can hamper the ability to take timely corrective action.
Interestingly, how quickly an organization responds to near miss reports can directly impact future incident rates. Companies that can address these concerns within a 24-hour period often observe a 25% decline in similar future incidents. Rapid responses not only indicate that safety issues are being taken seriously, but also can foster trust amongst the workforce in the reporting process itself.
One of the major benefits of near miss reporting is the potential for uncovering hidden hazards. A thorough root cause analysis can reveal issues that might otherwise go unnoticed, and which if left unresolved could escalate into more severe events. This emphasizes the importance of delving deeper into the underlying causes of near misses.
Sadly, underreporting is a major concern in many workplaces. Estimates show that as much as 90% of near misses go unreported. This implies a potentially deep-rooted cultural issue regarding safety communication and openness, which can severely hamper the effectiveness of any safety program.
But there's a strong economic argument for embracing near miss reporting. Organizations that diligently track and address these incidents can potentially cut future incident costs by up to 50%. This strong economic incentive can push companies to invest in and improve their reporting procedures.
Technology can be a catalyst for better near miss reporting. Using mobile apps for reporting can boost reporting rates by about 40%. Easy access and streamlined reporting encourage more workers to take part in safety initiatives.
Enhanced worker engagement can also directly impact hazard reduction. Companies that actively gather and react to near miss data often see workplace hazard reductions of around 30%. This link emphasizes the value of using data to drive safety improvements.
Leadership's role in the process can also have a significant effect on the success of near miss reporting. When leaders actively review and address the reported incidents, it's shown to increase reporting rates by up to 50%. It's a powerful signal to workers that their safety is truly valued, leading to a more positive and proactive safety culture.
Finally, training and education can play a crucial role in the effectiveness of near miss reporting programs. When organizations provide training that focuses specifically on the importance of near miss reporting, it's often linked to a 60% rise in the number of reports. This training empowers workers with the understanding that every near miss is a learning opportunity and helps to build a culture of proactive safety.
7 Key Performance Metrics Every Loss Control Academy Graduate Should Monitor in 2024 - Safety Training Compliance Percentage Across Departments
Understanding how well each department within a company adheres to safety training requirements, represented by the "Safety Training Compliance Percentage Across Departments," is fundamentally important for any comprehensive safety program. A huge chunk of organizations—a shocking 74%—struggle to effectively measure their progress against their safety goals. In this landscape, making sure everyone completes their required safety training becomes crucial to both minimizing risks and being in compliance with whatever rules they need to follow. When departments consistently reach high compliance rates with training, it typically leads to a safer work environment. So, by keeping close tabs on these compliance percentages, companies can easily identify areas where they might fall short and take the necessary corrective actions. Moreover, it's not enough to just train people once. Staying on top of expiring training certificates and making sure employees are retrained helps create a culture of ongoing safety improvement, a must in today’s quickly changing workplaces. Organizations that really focus on consistent compliance across all departments are taking a clear step toward making a strong culture of safety that, in the end, protects workers and helps the entire operation run better.
When examining workplace safety, it's crucial to understand how well different departments are adhering to safety training requirements. It's intriguing to see how widely these compliance rates can vary. For example, some departments like those involved in manufacturing or technical fields might only have around 50% of their employees complete required safety training, while administrative or office areas can often see rates as high as 90%. This disparity suggests that companies might need to tailor their training programs to meet the specific needs of different work groups.
The way training is presented can also have a significant impact. It appears that more engaging methods like hands-on training sessions or interactive workshops can boost compliance rates by as much as 30% compared to more traditional classroom styles. This highlights the importance of ensuring that training is designed to be relevant and interesting to those being trained.
Interestingly, there can also be seasonal trends in training compliance. For instance, when businesses are busy or facing deadlines, safety training completion tends to fall off. This could be due to a variety of reasons, like employees feeling pressed for time or even a reduced emphasis on safety during busy periods. Recognizing this pattern might allow companies to develop strategies to address it.
The link between safety training and actual workplace incidents is another important aspect to explore. Studies show that companies with a high rate of safety training compliance, upwards of 85%, tend to experience a reduction in workplace incidents—sometimes as much as 40%—compared to organizations with lower compliance. This implies a strong connection between employee knowledge of safety procedures and the likelihood of having fewer accidents.
The way companies deliver training is also evolving, with technology playing a larger role. For example, the use of mobile learning applications can boost compliance rates by about 25%. This makes sense given how much more convenient and accessible mobile training can be, particularly for workers who are frequently on the move.
The role of leadership in promoting safety training is also notable. It seems that when managers and supervisors actively take part in training sessions, compliance rates tend to go up by over 20%. This suggests that the emphasis leaders put on safety greatly affects how employees view training and their commitment to safety practices.
A significant concern, however, is the reliability of departmental self-reports on safety training compliance. Audits often reveal that the actual rates can be as much as 15% lower than what the departments report. This emphasizes the need for organizations to regularly audit these numbers to get a more accurate picture of the situation.
When staff members come and go frequently, like in seasonal or temporary positions, safety training compliance can be a challenge. For example, these employees might have rates that are around 30% lower compared to more permanent employees. This suggests a need for companies to have specific training procedures for these types of workers.
There's also a psychological element to safety training. It seems that employees are more likely to engage with safety training if they feel like they have a supportive work environment where their voices are heard and where they aren't afraid to bring up safety concerns. Companies with a positive work environment see compliance rates go up significantly, sometimes by 50%. This suggests that trust and openness within a company can play a large role in ensuring employees complete their safety training.
Finally, it's important to acknowledge that simply completing training isn't enough if employees don't retain what they learn. Research indicates that after a few months, workers can forget as much as 60% of the safety information they initially learned. Implementing refresher courses or ongoing reinforcement of key safety points might be a useful strategy to help employees retain that information and keep safety top of mind.
All of this information reveals that ensuring safety training compliance isn't just a matter of ticking boxes, but a complex and nuanced process that involves careful consideration of many factors—departmental differences, training formats, seasonal factors, technology, leadership involvement, and the psychology of the workplace. A thorough understanding of these factors is crucial for creating a safe and effective work environment.
7 Key Performance Metrics Every Loss Control Academy Graduate Should Monitor in 2024 - Risk Assessment Accuracy Rate vs Actual Loss Events
For loss control professionals, understanding how well risk assessments predict actual losses is a key aspect of their work. When risk assessments accurately identify potential hazards, organizations can take steps to minimize those risks. But relying solely on assessment accuracy can be misleading. The reality of actual loss events reminds us that even the most precise assessments may not always fully capture the complexities of risk. It's important to look at the differences between predicted risk and what actually happens in order to refine risk management practices. By consistently comparing the results of risk assessments to the actual occurrences of losses, professionals can uncover areas where the assessments fall short and improve future decision-making. This highlights the need for a more holistic approach in 2024 and beyond, one that combines statistical analysis with insights from human experience to create a more robust and effective risk management framework for any organization.
The effectiveness of risk assessments in predicting actual loss events is often surprisingly low, frequently falling below 65% accuracy across various industries. This suggests that even sophisticated risk assessment models may struggle to capture the complexities of real-world scenarios. It seems that relying too much on historical loss data can lead to a kind of tunnel vision, hindering the ability to identify emerging risks. This approach can create an accuracy gap of up to 40% in spotting future losses, especially in sectors undergoing rapid change.
Interestingly, human biases can also significantly influence the accuracy of risk assessments. Things like an overly optimistic outlook on safety or an overestimation of control can introduce error, lowering accuracy by as much as 30%. It’s fascinating how the accuracy of risk assessments can differ dramatically between industries. For example, industries like construction and manufacturing may see accuracy rates around 45%, while the financial services sector might achieve rates up to 75%. This underscores the need for tailoring risk management approaches to fit the unique challenges of each industry.
It's also intriguing to see how the speed of response to identified risks directly relates to the accuracy of the initial risk assessment. Organizations that are quick to act on risk assessment findings can often reduce future loss events by around 25% when compared to those that are slower to react. This highlights the importance of not just identifying risks, but also acting quickly on them.
Risk assessment frequency seems to be an important factor. Those companies that regularly—say quarterly—assess their risks may find their assessments are around 20% more accurate than those that only do it annually. This might suggest that risks are constantly evolving, and regular evaluations help to catch up with these changes. External forces, like changes in the economy or regulations, can significantly impact the accuracy of risk assessments. Studies indicate that accuracy can fall by as much as 50% during times of major external pressures. This indicates that risk assessment methods need to adapt in the face of major changes in the world outside the organization.
The use of newer technologies, such as machine learning algorithms, can have a positive impact on the accuracy of risk assessments. Some companies that have adopted these technologies have seen improvements in accuracy of up to 30%. This seems to suggest a future trend towards increasing reliance on advanced methods to assess and manage risks. However, there's a significant challenge in that as much as 70% of minor losses may go unreported. This underreporting can skew the results of any risk assessment and create an inaccurate picture of the actual risks that the organization faces. This points towards possible issues with workplace culture regarding safety and communication.
The way teams within an organization communicate about risk assessments can also be important. Effective communication and collaboration among departments can raise accuracy by around 25%. This suggests that ensuring everyone understands the risk assessments and how to respond is essential for maximizing the usefulness of those assessments. This is certainly an area for continued research to understand how to improve communication and collaboration.
7 Key Performance Metrics Every Loss Control Academy Graduate Should Monitor in 2024 - Employee Safety Behavior Observation Scores
Employee Safety Behavior Observation Scores provide a valuable way to gauge how well safety programs are working within an organization. These scores capture feedback on how employees are performing in relation to safety practices, which helps promote a proactive and safety-conscious workplace culture. Companies often set targets for the number of employees observed and the frequency of feedback, aiming to keep safety top of mind. While using metrics like these is important, it's crucial to remember that the actual quality of the observations and the circumstances under which they are made also have a big impact on the overall safety outcomes. Ultimately, these scores should be viewed as a guide for improvement, highlighting areas where safety protocols and employee training can be enhanced.
Employee Safety Behavior Observation Scores are becoming increasingly important in gauging safety performance. They put a spotlight on the value of feedback when it comes to what people do at work. Companies often set goals to observe and give feedback to a certain number of workers, hoping to encourage a culture where safety is always top of mind.
These kinds of scores are a good example of what researchers call a 'leading indicator'—they're useful for predicting future outcomes. In the field of safety, these kinds of metrics are essential for managing and making improvements. When we talk about 'key performance indicators' (KPIs) in safety, we're talking about ways to measure how safe a workplace is. These metrics need to be relevant and timely.
Training is also a big part of safety, so we look at things like how often and how long training sessions are. These are vital KPIs that tell us how much people know and if they're following the rules. Another metric is the number of safety observations submitted. This helps us understand if workers are actively looking for hazards and if the safety culture is improving.
Traditional metrics, called 'lagging indicators,' are also important. These tend to focus on things like the Recordable Injury Rate, which shows us the history of safety incidents and helps identify trends. For these metrics to be useful, we need to set standards to measure against and give ourselves a timeframe to achieve them.
Safety management systems often rely on various data sources for tracking these metrics, providing both manual and automated ways to produce reports. The ideal scenario involves looking at both leading and lagging indicators. By tracking both the past and trying to predict the future, organizations can continuously improve their safety efforts.
It's worth noting that, while observer scores are a valuable tool, they can be influenced by the individual doing the observation. Creating clear criteria and providing training to the observers can help minimize these biases. It is also vital to combine observation scores with other data points to build a more comprehensive view of safety performance, and not to rely solely on a single metric.
Despite the potential for bias, observation scores provide a window into employee actions and how safety procedures are followed in practice. Regularly analyzing these scores alongside other relevant data can help organizations address unsafe behavior and prevent incidents before they occur, thereby creating a safer and more productive work environment.
More Posts from insuranceanalysispro.com: